JIT与库存控制
20世纪70年代是企业以关注质量为特征的10年,在此期间,企业对“全面质量管理”和“零缺陷”之类的技术有着浓厚的兴趣。在20世纪80年代,质量不再是竞争力的一个来源,它被称为一种基本要求,没有质量,企业就无法生存。然后,竞争的重点转到了生产效率,比如“准时生产方式”和“零库存”生产方式开始形成。在20世纪90年代,大量的企业应用这些制造技术取得了成功。
准时生产方式(just in time,简称JIT)产生于1973年爆发的全球石油危机及由此所引起的日益严重的自然资源短缺,这对于当时靠进口原材料发展经济的日本冲击最大。生产制造类企业为了生存,在原材辑成本难以降低的情况下,只能从物流过程寻找利润源,减少采购、库存、运输等方面所产生的费用。准时生产方式这一思路最初由日本丰田公司提出并应用。20世纪80年代,西方发达国际逐渐重视对JIT技术的研究,并广泛应用于生产管理、物流管理等方面。JIT已从最初的一种减少库存水平的方法,发展成为一种内涵丰富,包括特定知识、原则、技术和方法的管理哲学。
一、JIT基本原理
JIT管理是指在精确测定生产制造各工艺环节作业效率的前提下,准确地计划物料供应量和供应时间的生产管理模式。其核心思想是“只在需要的时候,按照需要的数量,生产需要的产品”。具体而言,是指保证品种有效性,拒绝不需要的品种;保证数量有效性,拒绝多余的数量;保证所需的时间,拒绝不按时供应;保证产品质量,拒绝次品和废品。JIT的最终目标是一个平衡系统,一个贯穿整个系统的平滑、迅速的物料流。在该方式下,生产过程将在尽可能短的时间内,以尽可能最佳的方式利用资源,杜绝浪费。
在JIT理念中,浪费包括:过量生产,等侯时间,不必要的运输,存货,加工废品,工作方法低效和产品缺陷。特别地,JIT认为库存是万恶之源,因为它不仅占用大量的资金,造成修建或租赁仓库等一系列不增加价值的活动,产生浪费,而且还将许多管理不善的问题掩盖起来,如机器经常出故障,设备调整时间太长,设备能力不平衡,缺勤率高,备件供应不及时等,使问题得不到及时解决,JIT就是要通过不断减少库存来暴露管理中的问题,以不断消除根费,进行不断的改进。
尽管JIT的基本思想简单,容易理解,但是,实现JIT却不容易。JIT设置了一个最高境界,一种极限—“零库存”。实际生产只能无限接近这个极限,但却永远不可能达到。
#p#副标题#e#
二、JIT生产系统与需求管理
在库存控制方面,JIT不同于物科需求计划(MRP),后者被称为推动式系统。
1.拉动式系统
拉动式系统是指由市场需求信息拉动产品装配需求,再由产品装配需求拉动零件加工。每道工序和每个车间按照当时的需求向前一道工序和上游车间发出需求指令,上游工序和车间完全按这些需求指令进行生产,形成物流和信息流的统一。这种方式为拉动式方式。
2.推动式系统
推动式系统是指计划部门根据市场需求,按零部件展开,计算出每种零部件的需要量和需要时间,形成每个零部件的投入产出计划.然后将计划发给每一个生产
地和工作车间,每一个生产地和生产车间都按计划制造零部件,将实际完成情况反馈到计划部门,并将加工完的零部件达到后一道工序和下游生产车间,不管后一道工序和下游生产车间当时是否需要。这种方式为推动式方式。由于实际生产作业计划会不可避免地受到随机因素的干扰,因此推进式方式必然造成物流和信息流的分离。
3.需求管理
无论在拉动式系统还是在推动式系统中,使系统运行的动力都是需求,没有需求,系统就不会运行。拉动式系统中的需求是市场真实的需求,而推动式系统中的需求是计划部门预测的需求。因此在任何一种生产系统中都存在需求管理的问题。需求管理的任务是协调,控制各种需求的来源,从而有效地利用生产系统并能按时交付货物。
1)需求的空间和时间特征
需求随时间的变化归因于季节性的市场销售额的增长或下降等因素导致的一般性波动。需求有时间和空间两个维度,即需求管理者必须知道需求量在何时发生、何处发生。仓库位置规划、平衡物流网络中的库存水平、按地理位置分配运输资源等都需要知道需求的空间位置。
2)派生需求和独立需求
派生需求,也称为非独立需求,是指由对其他产品或服务的需求而引发的对此种产品或服务的需求,而独立需求和派生需求刚好相反。例如,如果一家汽车公司计划每天生产500辆汽车,那么很显然它将需要2000个汽车轮子和轮胎,那么对汽车轮子和轮胎的需求是派生需求,非独立的,依赖于汽车的需求量;而对于汽车的需求是独立的,它来自于汽车公司外部。
3)确定性需求和随机性需求
确定性需求,又称为规律性需求,是指市场对该产品的需求的数量随时间维度大致固定不变的,或者有变化,也呈现出规律性的波动,可以对其提前准确预测,随机性需求,也称为不规律需求,它和确定性需求刚好相反,市场对需求的数量不确定,而且其时间维度也没有规律性,一般很难准确预测。确定性需求的产品可以采用推进式系统,但随机性需求的产品需要采用拉动性系统。
#p#副标题#e#
三、JIT系统库存控制
JIT系统是一种典型的拉动式系统,市场对产品的需求是JIT系统员最头的拉动力,产品需求再引发对各种零部件和物料的需求。日本丰田公司最早发明了一种被命名为“看板拉动系统”的方法来控制JIT系统的库存。看板,在日文中意思是“信号”,是用来传递生产计划与控制信息的工具。看板一般分为两种:生产看板和搬运看板。生产看板用于指挥生产,规定了各工序应该生产的零部件种类和数量,生产看板一般是通过指挥放置零部件的容器的适时适量的补给来指挥JIT生产的。搬运看板是用于指挥零部件在前后两道工序之间的传送,即适时适量地将容器内的在制品传送到下游工序,一般容器内规定放置的零部件的数量是固定不变的。(如下图所示)
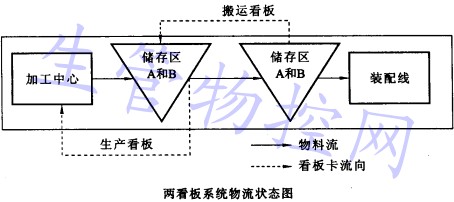
该图画出了一条装配线,该装配线由一个加工中心供应零件,该加工中心生产A和B两种零件,这两种零件储存在两个容器里,一种靠近装配线,另一种靠近加工中心,靠近装配线的容器内有一个搬运看板,靠近加工中心的容器内有一个生产看板。这就是通常所说的两看板系统。
当装配线从一个装满第一种零件A的容器中取走零件时,就有一个工人从容器中取走搬运看板,把这个看板放到加工中心的储存区。在加工中心,工人发现了零件A的容器,取出生产看板,并放入了搬运看板。容器中放入搬运看板就说明准许将该容器移送到装配线。而取出的生产看板则放在加工中心的工具架上,说明现在准许另一批原料投入生产。工具架上的看板就成为加工中心的分配表。
看板拉动方法不仅可以用于制造车间之内,也可以用于制造车间之间,还可以用于制造商和外部供应商之间,其原理都是一样的。
当市场需求发生改变时,就需要相应改变生产线的产出率,而只要对应改变生产看板和搬运看板的数量就能达到改变产出率的目的。因此确定JIT系统中的看板的数量就成为生产系统对市场需求响应的关键因家。与此同时,看板的数量也能决定JIT系统中在制品库存的数量,因为看板卡代表着使用区与供应区之间来回流动的物料的容器数,每个容器代表供应的最小生产批量,容器数量直接决定系统中的在制品的库存数。
精确地估计生产一个容器的零件所需的生产提前期是确定容器数量的关键所在。提前期与容器的零件加工时间、生产过程中的任何等待时间、将原料运送到工人手中所需运输时间有关系。看板数的计算公式如下:
K=(提前期内的期望需求量+安全库存量)/容器容量
=DL(1+S)/C
式中:K—看板数;
D—特定时段内所需产品的平均数量;
L—补充订货的提前期;
S—安全库存量,用提前期内需求量的百分比表示;
C—容器容量。
由此可见,看扳拉动系统并不能实现零库存,但是,它能控制一次投入工序中的物料数—通过控制每种零件的容器数来实现。可以方便地调整看板系统以适应系统当前的运行方式,因为看板卡片的数量可以十分容易地增加或减少,从而也达到了控制库存的目的,即根据市场的需求来决定生产系统库存数量,这样就完全没有多余的库存,减少了浪费。
#p#副标题#e#
例子:艾尔文汽车配件公司是为BigThree公司生产消音器组件的企业。该公司应用看板拉动的方式控制物料在其生产单元中的移动。每个生产单元被设计用来装配一种特定的消音器。消音器组件的装配包括切断和弯曲多根管子,再焊接到消音器和汽车的催化式排气净化器上等多项工作。消音器和净化器是基于当前的市场需求而拉入生产单元的。净化器在特定的生产单元中生产。
净化器以10个一瓶的方式进行生产,并用一种特殊的手推车运送到装配单元。净化器单元的设计是为了在实现零准备时间的前提下生产多种净化器,该单元每隔大约4小时对一批净化器的需求做出反应。因为净化器单元就位于消音器装配单元的旁边,因而可以实现运输时问为零。
消音器装配组装单元平均每小时大约装配8个组件,每个组件都使用同样的净化器。由于工序中多少存在差异,管理层确定需求量的10%作为安全库存。问需要多少看板数来管理净化器的供应任务,达到JIT的目标?
解 本例题中,供应净化器的提前期(L)为4小时,对净化器的需求(D)是每小时8个,安全库存(S)是期望需求的l0%,容器容量(C)是10单位,
则看板数K=8×4(1+0.1)÷10=3.52
本例中,需要4套看板,即需要在系统中设置4个装载净化器的容器容量是10个。
尽管利用JIT系统能准确做到“零库存”,但是通过上面的例题我们也可以看出,由于存在看板,生产过程中就不可能是零库存。如果单单从库存控制的角度来分析JIT,它和MRP系统下库存控制方法非常相似,都是从顾客的需求出发,来计划物料的订购数量和时间,都是从下道工序对上道工序的需求一步一步向源头迫近,也就是在生产过程中的每一道工序的存在都是因为有下一道工序的需求。唯一有差别的地方是JIT系统包括的内容更广泛,JIT系统不仅仅是一种生产技术,更是一种企业管理思想,包括了生产工艺和流程设计、全面质量管理、稳定的生产计划、看板控制系统、供应商合作思想、库存控制、改进产品设计等。
准时生产方式(just in time,简称JIT)产生于1973年爆发的全球石油危机及由此所引起的日益严重的自然资源短缺,这对于当时靠进口原材料发展经济的日本冲击最大。生产制造类企业为了生存,在原材辑成本难以降低的情况下,只能从物流过程寻找利润源,减少采购、库存、运输等方面所产生的费用。准时生产方式这一思路最初由日本丰田公司提出并应用。20世纪80年代,西方发达国际逐渐重视对JIT技术的研究,并广泛应用于生产管理、物流管理等方面。JIT已从最初的一种减少库存水平的方法,发展成为一种内涵丰富,包括特定知识、原则、技术和方法的管理哲学。
一、JIT基本原理
JIT管理是指在精确测定生产制造各工艺环节作业效率的前提下,准确地计划物料供应量和供应时间的生产管理模式。其核心思想是“只在需要的时候,按照需要的数量,生产需要的产品”。具体而言,是指保证品种有效性,拒绝不需要的品种;保证数量有效性,拒绝多余的数量;保证所需的时间,拒绝不按时供应;保证产品质量,拒绝次品和废品。JIT的最终目标是一个平衡系统,一个贯穿整个系统的平滑、迅速的物料流。在该方式下,生产过程将在尽可能短的时间内,以尽可能最佳的方式利用资源,杜绝浪费。
在JIT理念中,浪费包括:过量生产,等侯时间,不必要的运输,存货,加工废品,工作方法低效和产品缺陷。特别地,JIT认为库存是万恶之源,因为它不仅占用大量的资金,造成修建或租赁仓库等一系列不增加价值的活动,产生浪费,而且还将许多管理不善的问题掩盖起来,如机器经常出故障,设备调整时间太长,设备能力不平衡,缺勤率高,备件供应不及时等,使问题得不到及时解决,JIT就是要通过不断减少库存来暴露管理中的问题,以不断消除根费,进行不断的改进。
尽管JIT的基本思想简单,容易理解,但是,实现JIT却不容易。JIT设置了一个最高境界,一种极限—“零库存”。实际生产只能无限接近这个极限,但却永远不可能达到。
#p#副标题#e#
二、JIT生产系统与需求管理
在库存控制方面,JIT不同于物科需求计划(MRP),后者被称为推动式系统。
1.拉动式系统
拉动式系统是指由市场需求信息拉动产品装配需求,再由产品装配需求拉动零件加工。每道工序和每个车间按照当时的需求向前一道工序和上游车间发出需求指令,上游工序和车间完全按这些需求指令进行生产,形成物流和信息流的统一。这种方式为拉动式方式。
2.推动式系统
推动式系统是指计划部门根据市场需求,按零部件展开,计算出每种零部件的需要量和需要时间,形成每个零部件的投入产出计划.然后将计划发给每一个生产
地和工作车间,每一个生产地和生产车间都按计划制造零部件,将实际完成情况反馈到计划部门,并将加工完的零部件达到后一道工序和下游生产车间,不管后一道工序和下游生产车间当时是否需要。这种方式为推动式方式。由于实际生产作业计划会不可避免地受到随机因素的干扰,因此推进式方式必然造成物流和信息流的分离。
3.需求管理
无论在拉动式系统还是在推动式系统中,使系统运行的动力都是需求,没有需求,系统就不会运行。拉动式系统中的需求是市场真实的需求,而推动式系统中的需求是计划部门预测的需求。因此在任何一种生产系统中都存在需求管理的问题。需求管理的任务是协调,控制各种需求的来源,从而有效地利用生产系统并能按时交付货物。
1)需求的空间和时间特征
需求随时间的变化归因于季节性的市场销售额的增长或下降等因素导致的一般性波动。需求有时间和空间两个维度,即需求管理者必须知道需求量在何时发生、何处发生。仓库位置规划、平衡物流网络中的库存水平、按地理位置分配运输资源等都需要知道需求的空间位置。
2)派生需求和独立需求
派生需求,也称为非独立需求,是指由对其他产品或服务的需求而引发的对此种产品或服务的需求,而独立需求和派生需求刚好相反。例如,如果一家汽车公司计划每天生产500辆汽车,那么很显然它将需要2000个汽车轮子和轮胎,那么对汽车轮子和轮胎的需求是派生需求,非独立的,依赖于汽车的需求量;而对于汽车的需求是独立的,它来自于汽车公司外部。
3)确定性需求和随机性需求
确定性需求,又称为规律性需求,是指市场对该产品的需求的数量随时间维度大致固定不变的,或者有变化,也呈现出规律性的波动,可以对其提前准确预测,随机性需求,也称为不规律需求,它和确定性需求刚好相反,市场对需求的数量不确定,而且其时间维度也没有规律性,一般很难准确预测。确定性需求的产品可以采用推进式系统,但随机性需求的产品需要采用拉动性系统。
#p#副标题#e#
三、JIT系统库存控制
JIT系统是一种典型的拉动式系统,市场对产品的需求是JIT系统员最头的拉动力,产品需求再引发对各种零部件和物料的需求。日本丰田公司最早发明了一种被命名为“看板拉动系统”的方法来控制JIT系统的库存。看板,在日文中意思是“信号”,是用来传递生产计划与控制信息的工具。看板一般分为两种:生产看板和搬运看板。生产看板用于指挥生产,规定了各工序应该生产的零部件种类和数量,生产看板一般是通过指挥放置零部件的容器的适时适量的补给来指挥JIT生产的。搬运看板是用于指挥零部件在前后两道工序之间的传送,即适时适量地将容器内的在制品传送到下游工序,一般容器内规定放置的零部件的数量是固定不变的。(如下图所示)
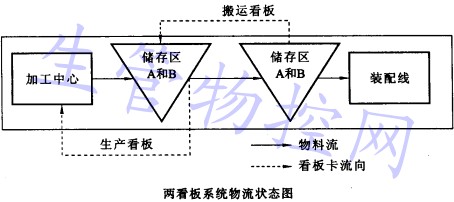
该图画出了一条装配线,该装配线由一个加工中心供应零件,该加工中心生产A和B两种零件,这两种零件储存在两个容器里,一种靠近装配线,另一种靠近加工中心,靠近装配线的容器内有一个搬运看板,靠近加工中心的容器内有一个生产看板。这就是通常所说的两看板系统。
当装配线从一个装满第一种零件A的容器中取走零件时,就有一个工人从容器中取走搬运看板,把这个看板放到加工中心的储存区。在加工中心,工人发现了零件A的容器,取出生产看板,并放入了搬运看板。容器中放入搬运看板就说明准许将该容器移送到装配线。而取出的生产看板则放在加工中心的工具架上,说明现在准许另一批原料投入生产。工具架上的看板就成为加工中心的分配表。
看板拉动方法不仅可以用于制造车间之内,也可以用于制造车间之间,还可以用于制造商和外部供应商之间,其原理都是一样的。
当市场需求发生改变时,就需要相应改变生产线的产出率,而只要对应改变生产看板和搬运看板的数量就能达到改变产出率的目的。因此确定JIT系统中的看板的数量就成为生产系统对市场需求响应的关键因家。与此同时,看板的数量也能决定JIT系统中在制品库存的数量,因为看板卡代表着使用区与供应区之间来回流动的物料的容器数,每个容器代表供应的最小生产批量,容器数量直接决定系统中的在制品的库存数。
精确地估计生产一个容器的零件所需的生产提前期是确定容器数量的关键所在。提前期与容器的零件加工时间、生产过程中的任何等待时间、将原料运送到工人手中所需运输时间有关系。看板数的计算公式如下:
K=(提前期内的期望需求量+安全库存量)/容器容量
=DL(1+S)/C
式中:K—看板数;
D—特定时段内所需产品的平均数量;
L—补充订货的提前期;
S—安全库存量,用提前期内需求量的百分比表示;
C—容器容量。
由此可见,看扳拉动系统并不能实现零库存,但是,它能控制一次投入工序中的物料数—通过控制每种零件的容器数来实现。可以方便地调整看板系统以适应系统当前的运行方式,因为看板卡片的数量可以十分容易地增加或减少,从而也达到了控制库存的目的,即根据市场的需求来决定生产系统库存数量,这样就完全没有多余的库存,减少了浪费。
#p#副标题#e#
例子:艾尔文汽车配件公司是为BigThree公司生产消音器组件的企业。该公司应用看板拉动的方式控制物料在其生产单元中的移动。每个生产单元被设计用来装配一种特定的消音器。消音器组件的装配包括切断和弯曲多根管子,再焊接到消音器和汽车的催化式排气净化器上等多项工作。消音器和净化器是基于当前的市场需求而拉入生产单元的。净化器在特定的生产单元中生产。
净化器以10个一瓶的方式进行生产,并用一种特殊的手推车运送到装配单元。净化器单元的设计是为了在实现零准备时间的前提下生产多种净化器,该单元每隔大约4小时对一批净化器的需求做出反应。因为净化器单元就位于消音器装配单元的旁边,因而可以实现运输时问为零。
消音器装配组装单元平均每小时大约装配8个组件,每个组件都使用同样的净化器。由于工序中多少存在差异,管理层确定需求量的10%作为安全库存。问需要多少看板数来管理净化器的供应任务,达到JIT的目标?
解 本例题中,供应净化器的提前期(L)为4小时,对净化器的需求(D)是每小时8个,安全库存(S)是期望需求的l0%,容器容量(C)是10单位,
则看板数K=8×4(1+0.1)÷10=3.52
本例中,需要4套看板,即需要在系统中设置4个装载净化器的容器容量是10个。
尽管利用JIT系统能准确做到“零库存”,但是通过上面的例题我们也可以看出,由于存在看板,生产过程中就不可能是零库存。如果单单从库存控制的角度来分析JIT,它和MRP系统下库存控制方法非常相似,都是从顾客的需求出发,来计划物料的订购数量和时间,都是从下道工序对上道工序的需求一步一步向源头迫近,也就是在生产过程中的每一道工序的存在都是因为有下一道工序的需求。唯一有差别的地方是JIT系统包括的内容更广泛,JIT系统不仅仅是一种生产技术,更是一种企业管理思想,包括了生产工艺和流程设计、全面质量管理、稳定的生产计划、看板控制系统、供应商合作思想、库存控制、改进产品设计等。