MRP与库存控制
物料需求计划(material requirements planning,MRP)起源于20世纪60年代初,最初是针对当时制造企业生产管理中存在的普遍问题以及传统库存控制方法的不足而提出的一种生产组织管理技术。它是一种生产计划与控制技术,以控制整个生产过程中的库存水平为出发点,围绕物料为中心组织生产的一种新的生产方式,也是一种新的库存控制思想。
一、订货点法的缺陷
订货点法是传统的库存计划与控制方法,其基本思想是根据过去的经验预测未来的需求,根据物料的需求情况来确定订货点和订货批量。
订货点法的基本假设点是:①对各种物料的需求是相互独立的;②物料的需求是稳定、连续的;③订货提前期是已知的、固定的。
订货点法适合于需求比较稳定的物料库存控制与管理。然而,在实际生产中,随着市场环境发生变化,需求常常是不稳定的、不均匀的,在这种情况下使用订货点法便暴露出一些明显的缺陷。
1.盲目性
由于需求的不均匀以及对需求的情况不了解,企业不得不保持一个较大数量的安全库存来应付这种需求。这样盲目地维持一定量的库存会造成资金积压,产生浪费。例如,对某种零件的需求可能有如下表所示的三种情况,假定通过经济订货批量计算出该零件的订货批量为50件。那么,对于情况1,第1周需要10件,若一次订50件,则余下40件还需存放9周,但到第10周真正需要时,余下的40件又不够,必须再次订货50件。同样地,对于情况2和情况3也存在类似情况。
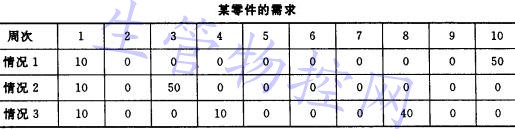
2.高库存与低服务水平
传统的订货点方法使得低库存与高服务水平两者不可兼得。一般认为,要达到高服务水平,则必须保持高库存,即使高库存也还会常常造成零件积压与短缺共存的局面。例如:如果装配一个部件,需要5个零件,当以95%的服务水平供给每种零件时,每种零件的库存水平很高。装配该部件时,5种零件都不发生缺货的概率是(0.95)5=0.774,大致每4次就有一次会发生缺货。
3.形成“块状”需求
订货点法的假设条件是均匀需求,但在制造过程中物料的需求是块状的:不需要的时候为零,需要时为一批。采用订货点法加剧了这种不均匀性。企业的产品、
零部件和原材料都采用订货点法进行控制,一般来说,市场对产品的需求较稳定,呈小锯齿状。当产品的库存下降到订货点以下时,企业开始组织该产品的装配。当装配产品时,必须从零部件库中取出各种零部件,这样,零部件库存徒然下降一块,当没达到零部件订货点时,零部件不必订货,这时原材料也不必订货。随着产品库存再次下降到订货点以下,再次需要进行产品的装配时,又要消耗一部分零部件的库存,如果零部件库存量下降到订货点以下,就要组织资源进行零部件的加工,要进行零部件的生产就要从原材料库中领取原材料,致使原材料库存降到订货点以下。由此可以看出,在产品的需求率均匀的条件下,由于采用订货点方法,造成对零件和原材料的需求率不均匀,呈“块状”。“块状”需求与“锯齿状”需求相比,平均库存水平几乎提高一倍,因而占用了更多的资金。
订货点法之所以有这些缺陷,是因为它没有按照各种物料真正需用的时间来确定订货日期。于是,人们便思考:怎样才能在需要的时间,按需要的数量得到真正需要的物料,从而消除盲目性,实现低库存与高服务水乎?
#p#副标题#e#
二、MRP的基本思想
物料需求计划(material requirement planning,MRP)是当时库存管理专家们为解决传统库存控制方法的不足,在不断探索新的库存控制方法的过程中产生的。最早提出解决方案的是美国IBM公司的J.A.奥列基博士,他在20世纪60年代设计并组织实施了第一个MRP系统。
MPR的基本思想是围绕物料转化组织制造资源,实现按需要准时生产。
制造型企业的生产是将原材料转化为产品的过程。如加工装配式生产,工艺顺序如下图所示,即;将原材料制成毛坯,毛坯加工成零件,零件组装成部件,部件总装成产品。对于制造型的流程工业,也具有类似生产工艺顺序的情况。

按上述的生产过程,如果确定了产品的需求时间和需求数量,就可以确定产品装配数量和装配时间。确定了产品装配数量和装配时间就可以按产品的结构确定产品所需的零部件的出产数量和出产时间,进而可以确定出零部件投入数量和投入时间,直至原材料需要的数量和需要的时间,汇总得出所需的制造资源和需要时间。(如下图所示)
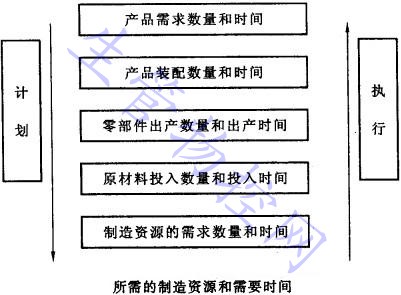
可见,MRP是以物料为中心来组织生产,以物料为中心体现了为顾客服务的宗旨和按需定产的思想。达里,“物料”是一个广义的概念,泛指原材料、在制品、外购件以及产品。以物料为中心组织生产,要求上道工序应该按下道工序的需求进行生产,前一生产阶段应该为后一生产阶段服务,各道工序做到既不提前完工,也不误期完工,因而是最经济的生产方式。MRP正是按这样的方式来完成各种生产作业计划的编制的。
MRP处理的是相关需求。在MRP中,将所有物料分成独立需求(independent demand)和相关需求(dependent demand)两种类型。独立需求就是指需求时间由企业外部的需求来决定,如客户订购的产品、售后服务用的备品备件等。其需求数量一般通过预测和订单来确定,可按订货点方法处理。相关需求则是指对某些项目的需求取决于对另一些项目的需求,如汽车制造中的轮胎需求,它取决于制造装配汽车的数量。相关需求一般发生在制造过程中,可以通过计算得到。对原材料、毛坯、零件、部件的需求,来自制造过程,是相关需求,MRP处理的正是这类相关需求。
从上可以看出,MRP思想的提出解决了物料转化过程中的几个关键问题:何时需要,需要什么,需要多少。它不仅在数量上解决了缺料问题,更关键的是从时间上来解决缺料问题。#p#副标题#e#
如果一个企业的经营活动从产品销售到原材料采购,从自制零件的加工到外协零件的供应,从工具和工艺装备的准备维修,从人员的安排到资金的筹措与运用,都围绕MRP的这种基本思想进行,就可以形成一整套新的方法体系,它涉及企业的每一个部门、每一项活动。因此,人们又将MRP看成是一种新的生产方式。
1.MRP的处理逻辑
MRP基本原理就是由产品的交货期展开成零部件的生产进度日程,和原材料、外购件的需求数量和需求日期。MRP的处理逻辑是:通过主生产计划明确“我们要制造什么?”要制造必须有相应的物料,因此通过物料清单明确“我们需要什么?”而需要的物料可能已经存放在仓库中,因此,要通过库存信息了解“我们已有什么?”通过MRP的处理,可以得出生产作业计划和采购计划。在生产作业计划中,规定了每一项自制件的需求数量、开工日期和完工日期,在采购计划中,规定了每一项外购物料的需求品种、需求数量、订货日期和到货日期。(如下图所示)
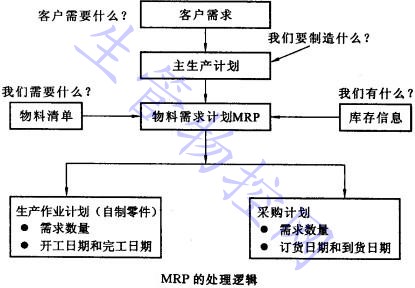
具体地,MRP需要处理的问题以及所需要的信息如下表所示。
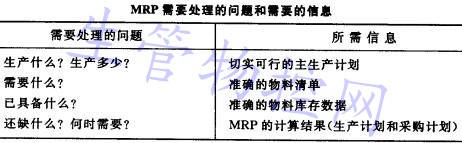
2.MBP的输入信息
通过上述的MRP的处理逻辑,可以看出MRP涉及三个输入信息:主生产计划(master product schedule,MPS)、物料清单(bill of materials,BOM)和库存状态文件。
(1)主生产计划(MPS),是MRP的主要输入,它是MRP运行的驱动力量,在MPS中列出的是企业向外界提供的产品等。
(2)物料清单(BOM),表示了产品的组成及结构信息,包括所需零部件的清单、产品项目的结构层次、制成最终产品的各个工艺阶段的先后顺序。
(3)库存状态文件,保存了每一种物料的有关数据,MRP系统关于订购什么、订购多少、何时发出订购等重要信息。物料清单是相对稳定的,而库存状态文件却处于不断变动之中。
3.MBP的输出信息
MRP的输出信息较多,其中关键的是生产和库存控制用的计划和报告。
(1)零部件投入出产计划。零部件投入出产计划规定了每个零件和部件的投入数量和投入时间,出产数量和出产时间。
(2)原材料需求计划。规定了每个零件所需的原材料的种类、需要数量和需要时间,并按原材料的品种、型号、规格汇总,以便物资部门进行采购。
(3)库存状态记录。记录各种零部件、外购件以及原材料的库存状态数据,以便于计划与实际的对比,进行生产进度控制和采购计划控制。
#p#副标题#e#
三、MRP系统下库存控制
下面举一个简单的例子来说明MRP系统的库存控制思想。如下表所示数据,在MRP系统中,物料的库存状态数据包括库存量、预计入库量、毛需求量、净需求量。
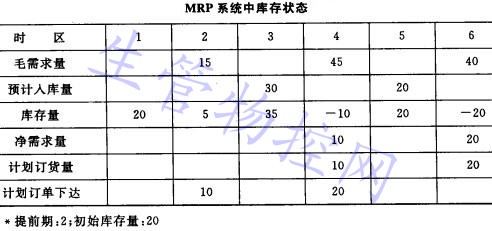
在上表的MRP系统中,时区2、4和6有收到顾客的需求,通过检查预计入库量、现库存量,得出净需求量,这个数量就是我们需要再订购的数量,同时由于订货存在提前期,所以尽管在时区4和6分别需要10单位和20单位物料,但仍然需要在时区2和4下达订单。这样就确定了两个问题,一是下达订单的时间,即时区2和4,二是确定了一次订单的数量,时区2的订单数量是l0单位,时区4的订单数量是20单位。这样综合考虑了再订购的数量和时间,以及库存量等因素,可以保证满足顾客在特定的时间需要特定数量的商品,而且也没有造成库存量的额外增加。MRP系统的库存控制思想实质就是根据需求来决定订货的数量和时间,整个生产过程没有产生新的库存。
在以上过程中,假定初始库存量为零,一样不会影响顾客需求的满足,只是改变订货的时间和数量。但是为什么MRP系统不能做到“零库存”呢?因为MRP系统存在两个很关键的问题,一是订货提前期,我们总是假定提前期总是固定的,因而MRP系统总是可以准确地确定出再订货的时间,不会造成早订货,物料积压,库存增加,但是,实践中由于并不能完全保证提前期是固定不变的,因此为了应对变化的提前期,就需要在库存中增加一些数量,预防在规定的提前期内物科没有及时到达,造成不能按时完成生产,顾客的需求得不到满足;另一个原因是MRP系统没有考虑生产能力的状况,尽管再订货的数量和时间能够准确确定,但是,如果在一段时间内.即使预定数量物料按时到达,但由于企业的生产能力受到限制,仍然不能满足顾客的需求,这时就需要保持一定的库存,来平衡生产能力,让设备能够在一定时间内保持均衡的产出。
#p#副标题#e#
四、MRP的发展
MRP的发展经历了从订货点法到MRP,从MRP到闭环MRP,再到同MRPⅡ和ERP的阶段。
1.闭环MRP(closed-loop MRP)
闭环MRP与MRP的最大区别在于闭环MRP增加了能力计划平衡功能。在MRP中,尽管按MRP的处理逻辑可以形成车间生产计划和采购计划,但车间生产计划和采购计划的可执行性很大程度上取决于车间生产能力的约束以及采购仓储的限制。为此,必须进行能力需求计划的平衡。如果能力需求计划可行,那么就可执行相应的能力计划和物料需求计划,否则,必须重新调整主生产计划和物料需求计划,使计划具有可行性,这样,形成一个计划与控制系统。总的来说,闭环MRP在初期MRP的基础上补充了以下功能。
(1)编制能力需求计划。
(2)建立了信息反馈机制,使计划部门能及时从供应商、车间作业现场、库房管理员、生产计划员那里了解计划的实际执行情况。
(3)计划调整功能。
2.制造资源计划(manufacturing resources planning,MRPⅡ)
制造资源计划是20世纪80年代初在MRP的基础上开始发展起来的,它是一种资源协调系统,代表了一种新的生产管理思想。
MRPⅡ的基本思想就是把企业看做一个有机整体,MRNⅡ实际上从横向和纵向两个角度体现了其管理思想。在纵向上,一方面向下体现出:从决策层、计划层到控制执行层对企业经营计划的层层分解,迅速下达,并具体落实到车间和班组,责任明确;另一方面,通过向上反映,从控制执行层、计划层到决策的计划执行情况信息的及时反馈,为计划的及时调整提供依据。在横向上,体现出企业的核心业务—“计划控制系统与财务系统”的集成关系,它们之间的联系桥梁是信息的管理—生产基础数据的管理。通过信息系统将基础数据集成为一体,实现企业各部门业务活动的沟通与联系,形成了一个资金流、物流、人员流相信息流的集成系统。
3.企业资源计划(enterprise resource planning,ERP)
企业资源计划是由美国著名的加特纳公司于20世纪90年代初提出的一个概念,它通过一系列的功能标准来界定ERP系统。由于企业的生产经营活动—从原材料的采购、制造到产品的分销不仅需要对企业内部资源进行计划控制,同时也需要外部企业的密切合作,而MRPⅡ仅局限于企业内物流、资金流和信息流的管理,由此产生了企业资源计划的概念。企业资源计划将企业的运营流程当做一条紧密连接的供应链,将企业链上的所有环节集成为一体化系统,实施有效管理。与MRPⅡ相比较,ERP具有如下的功能特点。
1)扩充了企业经营管理功能ERP相对于MRPⅡ,在原有功能的基础上进行了拓宽,增加了质量控制、运输、分销、售后服务与维护、市场开发、人事管理、实验室管理、项目管理、配方管理、融资投资管理、获利分析、经营风险管理等功能子系统。它可以实现全球范围内的多工厂、多地点的跨国经营动作。
2)面向供应链—扩充了企业经营管理的范围
ERP系统把客户需求和企业内部制造活动以及供应商的制造资源整合在一起,强调对供应链上所有环节进行有效管理。
3)模拟分析和决策支持的扩展—支持动态的监控能力
为企业制订计划和进行决策提供多种模拟功能和财务决策支持系统,提供诸如产品、融资投资、风险、企业合并、收购等决策分析功能,在企业级的范围内提供了对质量、客户满意、绩效等关俊问题的实时分析能力。
4)系统功能模块化
运用应用程序模块来对供应链上的所有环节实施有效管理。“物流”类模块对供应、生产、销售整个过程和各个环节所需的物料进行管理。“财务”类模块提供一套通用记账系统,它能够进行资产管理,提供有关经营成果的报告,使企业管理决策建立在客观、及时的信息基础之上。“人力资源”类模块提供一个综合的人力资源管理系统。它综合了诸如人事计划、新员工招聘、工资管理和员工个人发展等各项业务活动。
一、订货点法的缺陷
订货点法是传统的库存计划与控制方法,其基本思想是根据过去的经验预测未来的需求,根据物料的需求情况来确定订货点和订货批量。
订货点法的基本假设点是:①对各种物料的需求是相互独立的;②物料的需求是稳定、连续的;③订货提前期是已知的、固定的。
订货点法适合于需求比较稳定的物料库存控制与管理。然而,在实际生产中,随着市场环境发生变化,需求常常是不稳定的、不均匀的,在这种情况下使用订货点法便暴露出一些明显的缺陷。
1.盲目性
由于需求的不均匀以及对需求的情况不了解,企业不得不保持一个较大数量的安全库存来应付这种需求。这样盲目地维持一定量的库存会造成资金积压,产生浪费。例如,对某种零件的需求可能有如下表所示的三种情况,假定通过经济订货批量计算出该零件的订货批量为50件。那么,对于情况1,第1周需要10件,若一次订50件,则余下40件还需存放9周,但到第10周真正需要时,余下的40件又不够,必须再次订货50件。同样地,对于情况2和情况3也存在类似情况。
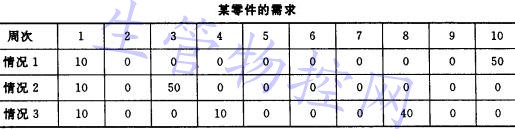
2.高库存与低服务水平
传统的订货点方法使得低库存与高服务水平两者不可兼得。一般认为,要达到高服务水平,则必须保持高库存,即使高库存也还会常常造成零件积压与短缺共存的局面。例如:如果装配一个部件,需要5个零件,当以95%的服务水平供给每种零件时,每种零件的库存水平很高。装配该部件时,5种零件都不发生缺货的概率是(0.95)5=0.774,大致每4次就有一次会发生缺货。
3.形成“块状”需求
订货点法的假设条件是均匀需求,但在制造过程中物料的需求是块状的:不需要的时候为零,需要时为一批。采用订货点法加剧了这种不均匀性。企业的产品、
零部件和原材料都采用订货点法进行控制,一般来说,市场对产品的需求较稳定,呈小锯齿状。当产品的库存下降到订货点以下时,企业开始组织该产品的装配。当装配产品时,必须从零部件库中取出各种零部件,这样,零部件库存徒然下降一块,当没达到零部件订货点时,零部件不必订货,这时原材料也不必订货。随着产品库存再次下降到订货点以下,再次需要进行产品的装配时,又要消耗一部分零部件的库存,如果零部件库存量下降到订货点以下,就要组织资源进行零部件的加工,要进行零部件的生产就要从原材料库中领取原材料,致使原材料库存降到订货点以下。由此可以看出,在产品的需求率均匀的条件下,由于采用订货点方法,造成对零件和原材料的需求率不均匀,呈“块状”。“块状”需求与“锯齿状”需求相比,平均库存水平几乎提高一倍,因而占用了更多的资金。
订货点法之所以有这些缺陷,是因为它没有按照各种物料真正需用的时间来确定订货日期。于是,人们便思考:怎样才能在需要的时间,按需要的数量得到真正需要的物料,从而消除盲目性,实现低库存与高服务水乎?
#p#副标题#e#
二、MRP的基本思想
物料需求计划(material requirement planning,MRP)是当时库存管理专家们为解决传统库存控制方法的不足,在不断探索新的库存控制方法的过程中产生的。最早提出解决方案的是美国IBM公司的J.A.奥列基博士,他在20世纪60年代设计并组织实施了第一个MRP系统。
MPR的基本思想是围绕物料转化组织制造资源,实现按需要准时生产。
制造型企业的生产是将原材料转化为产品的过程。如加工装配式生产,工艺顺序如下图所示,即;将原材料制成毛坯,毛坯加工成零件,零件组装成部件,部件总装成产品。对于制造型的流程工业,也具有类似生产工艺顺序的情况。

按上述的生产过程,如果确定了产品的需求时间和需求数量,就可以确定产品装配数量和装配时间。确定了产品装配数量和装配时间就可以按产品的结构确定产品所需的零部件的出产数量和出产时间,进而可以确定出零部件投入数量和投入时间,直至原材料需要的数量和需要的时间,汇总得出所需的制造资源和需要时间。(如下图所示)
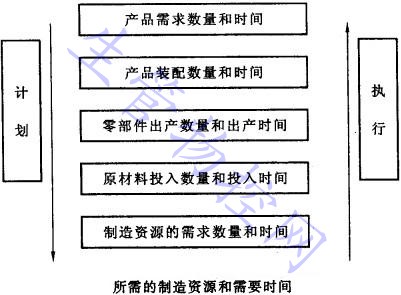
可见,MRP是以物料为中心来组织生产,以物料为中心体现了为顾客服务的宗旨和按需定产的思想。达里,“物料”是一个广义的概念,泛指原材料、在制品、外购件以及产品。以物料为中心组织生产,要求上道工序应该按下道工序的需求进行生产,前一生产阶段应该为后一生产阶段服务,各道工序做到既不提前完工,也不误期完工,因而是最经济的生产方式。MRP正是按这样的方式来完成各种生产作业计划的编制的。
MRP处理的是相关需求。在MRP中,将所有物料分成独立需求(independent demand)和相关需求(dependent demand)两种类型。独立需求就是指需求时间由企业外部的需求来决定,如客户订购的产品、售后服务用的备品备件等。其需求数量一般通过预测和订单来确定,可按订货点方法处理。相关需求则是指对某些项目的需求取决于对另一些项目的需求,如汽车制造中的轮胎需求,它取决于制造装配汽车的数量。相关需求一般发生在制造过程中,可以通过计算得到。对原材料、毛坯、零件、部件的需求,来自制造过程,是相关需求,MRP处理的正是这类相关需求。
从上可以看出,MRP思想的提出解决了物料转化过程中的几个关键问题:何时需要,需要什么,需要多少。它不仅在数量上解决了缺料问题,更关键的是从时间上来解决缺料问题。#p#副标题#e#
如果一个企业的经营活动从产品销售到原材料采购,从自制零件的加工到外协零件的供应,从工具和工艺装备的准备维修,从人员的安排到资金的筹措与运用,都围绕MRP的这种基本思想进行,就可以形成一整套新的方法体系,它涉及企业的每一个部门、每一项活动。因此,人们又将MRP看成是一种新的生产方式。
1.MRP的处理逻辑
MRP基本原理就是由产品的交货期展开成零部件的生产进度日程,和原材料、外购件的需求数量和需求日期。MRP的处理逻辑是:通过主生产计划明确“我们要制造什么?”要制造必须有相应的物料,因此通过物料清单明确“我们需要什么?”而需要的物料可能已经存放在仓库中,因此,要通过库存信息了解“我们已有什么?”通过MRP的处理,可以得出生产作业计划和采购计划。在生产作业计划中,规定了每一项自制件的需求数量、开工日期和完工日期,在采购计划中,规定了每一项外购物料的需求品种、需求数量、订货日期和到货日期。(如下图所示)
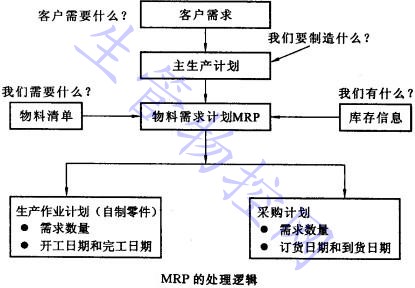
具体地,MRP需要处理的问题以及所需要的信息如下表所示。
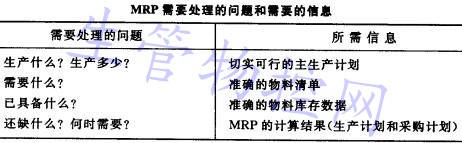
2.MBP的输入信息
通过上述的MRP的处理逻辑,可以看出MRP涉及三个输入信息:主生产计划(master product schedule,MPS)、物料清单(bill of materials,BOM)和库存状态文件。
(1)主生产计划(MPS),是MRP的主要输入,它是MRP运行的驱动力量,在MPS中列出的是企业向外界提供的产品等。
(2)物料清单(BOM),表示了产品的组成及结构信息,包括所需零部件的清单、产品项目的结构层次、制成最终产品的各个工艺阶段的先后顺序。
(3)库存状态文件,保存了每一种物料的有关数据,MRP系统关于订购什么、订购多少、何时发出订购等重要信息。物料清单是相对稳定的,而库存状态文件却处于不断变动之中。
3.MBP的输出信息
MRP的输出信息较多,其中关键的是生产和库存控制用的计划和报告。
(1)零部件投入出产计划。零部件投入出产计划规定了每个零件和部件的投入数量和投入时间,出产数量和出产时间。
(2)原材料需求计划。规定了每个零件所需的原材料的种类、需要数量和需要时间,并按原材料的品种、型号、规格汇总,以便物资部门进行采购。
(3)库存状态记录。记录各种零部件、外购件以及原材料的库存状态数据,以便于计划与实际的对比,进行生产进度控制和采购计划控制。
#p#副标题#e#
三、MRP系统下库存控制
下面举一个简单的例子来说明MRP系统的库存控制思想。如下表所示数据,在MRP系统中,物料的库存状态数据包括库存量、预计入库量、毛需求量、净需求量。
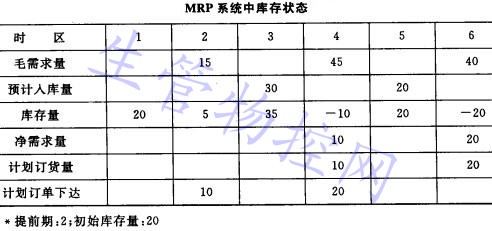
在上表的MRP系统中,时区2、4和6有收到顾客的需求,通过检查预计入库量、现库存量,得出净需求量,这个数量就是我们需要再订购的数量,同时由于订货存在提前期,所以尽管在时区4和6分别需要10单位和20单位物料,但仍然需要在时区2和4下达订单。这样就确定了两个问题,一是下达订单的时间,即时区2和4,二是确定了一次订单的数量,时区2的订单数量是l0单位,时区4的订单数量是20单位。这样综合考虑了再订购的数量和时间,以及库存量等因素,可以保证满足顾客在特定的时间需要特定数量的商品,而且也没有造成库存量的额外增加。MRP系统的库存控制思想实质就是根据需求来决定订货的数量和时间,整个生产过程没有产生新的库存。
在以上过程中,假定初始库存量为零,一样不会影响顾客需求的满足,只是改变订货的时间和数量。但是为什么MRP系统不能做到“零库存”呢?因为MRP系统存在两个很关键的问题,一是订货提前期,我们总是假定提前期总是固定的,因而MRP系统总是可以准确地确定出再订货的时间,不会造成早订货,物料积压,库存增加,但是,实践中由于并不能完全保证提前期是固定不变的,因此为了应对变化的提前期,就需要在库存中增加一些数量,预防在规定的提前期内物科没有及时到达,造成不能按时完成生产,顾客的需求得不到满足;另一个原因是MRP系统没有考虑生产能力的状况,尽管再订货的数量和时间能够准确确定,但是,如果在一段时间内.即使预定数量物料按时到达,但由于企业的生产能力受到限制,仍然不能满足顾客的需求,这时就需要保持一定的库存,来平衡生产能力,让设备能够在一定时间内保持均衡的产出。
#p#副标题#e#
四、MRP的发展
MRP的发展经历了从订货点法到MRP,从MRP到闭环MRP,再到同MRPⅡ和ERP的阶段。
1.闭环MRP(closed-loop MRP)
闭环MRP与MRP的最大区别在于闭环MRP增加了能力计划平衡功能。在MRP中,尽管按MRP的处理逻辑可以形成车间生产计划和采购计划,但车间生产计划和采购计划的可执行性很大程度上取决于车间生产能力的约束以及采购仓储的限制。为此,必须进行能力需求计划的平衡。如果能力需求计划可行,那么就可执行相应的能力计划和物料需求计划,否则,必须重新调整主生产计划和物料需求计划,使计划具有可行性,这样,形成一个计划与控制系统。总的来说,闭环MRP在初期MRP的基础上补充了以下功能。
(1)编制能力需求计划。
(2)建立了信息反馈机制,使计划部门能及时从供应商、车间作业现场、库房管理员、生产计划员那里了解计划的实际执行情况。
(3)计划调整功能。
2.制造资源计划(manufacturing resources planning,MRPⅡ)
制造资源计划是20世纪80年代初在MRP的基础上开始发展起来的,它是一种资源协调系统,代表了一种新的生产管理思想。
MRPⅡ的基本思想就是把企业看做一个有机整体,MRNⅡ实际上从横向和纵向两个角度体现了其管理思想。在纵向上,一方面向下体现出:从决策层、计划层到控制执行层对企业经营计划的层层分解,迅速下达,并具体落实到车间和班组,责任明确;另一方面,通过向上反映,从控制执行层、计划层到决策的计划执行情况信息的及时反馈,为计划的及时调整提供依据。在横向上,体现出企业的核心业务—“计划控制系统与财务系统”的集成关系,它们之间的联系桥梁是信息的管理—生产基础数据的管理。通过信息系统将基础数据集成为一体,实现企业各部门业务活动的沟通与联系,形成了一个资金流、物流、人员流相信息流的集成系统。
3.企业资源计划(enterprise resource planning,ERP)
企业资源计划是由美国著名的加特纳公司于20世纪90年代初提出的一个概念,它通过一系列的功能标准来界定ERP系统。由于企业的生产经营活动—从原材料的采购、制造到产品的分销不仅需要对企业内部资源进行计划控制,同时也需要外部企业的密切合作,而MRPⅡ仅局限于企业内物流、资金流和信息流的管理,由此产生了企业资源计划的概念。企业资源计划将企业的运营流程当做一条紧密连接的供应链,将企业链上的所有环节集成为一体化系统,实施有效管理。与MRPⅡ相比较,ERP具有如下的功能特点。
1)扩充了企业经营管理功能ERP相对于MRPⅡ,在原有功能的基础上进行了拓宽,增加了质量控制、运输、分销、售后服务与维护、市场开发、人事管理、实验室管理、项目管理、配方管理、融资投资管理、获利分析、经营风险管理等功能子系统。它可以实现全球范围内的多工厂、多地点的跨国经营动作。
2)面向供应链—扩充了企业经营管理的范围
ERP系统把客户需求和企业内部制造活动以及供应商的制造资源整合在一起,强调对供应链上所有环节进行有效管理。
3)模拟分析和决策支持的扩展—支持动态的监控能力
为企业制订计划和进行决策提供多种模拟功能和财务决策支持系统,提供诸如产品、融资投资、风险、企业合并、收购等决策分析功能,在企业级的范围内提供了对质量、客户满意、绩效等关俊问题的实时分析能力。
4)系统功能模块化
运用应用程序模块来对供应链上的所有环节实施有效管理。“物流”类模块对供应、生产、销售整个过程和各个环节所需的物料进行管理。“财务”类模块提供一套通用记账系统,它能够进行资产管理,提供有关经营成果的报告,使企业管理决策建立在客观、及时的信息基础之上。“人力资源”类模块提供一个综合的人力资源管理系统。它综合了诸如人事计划、新员工招聘、工资管理和员工个人发展等各项业务活动。